Horlecke 11 in Menden , Germany
(geo-cluster West Europe)
Menden is located in the mid-west of Germany at 30 kilometres distance to Dortmund city.
The office building was presumably erected between 1910 and 1930. It is part of an industrial area containing mostly storehouses and manufacturing companies. The building is attached to the neighbour buildings that are aligned on the street side. The office is a 1 storey building with basement and has a footprint of 187 m² and a gross volume of 744 m³. The actual energy consumption is 258 kWh/ m²a. It is a part of a huge complex on one site with a usable space of approximately 4.000 m².
Building structure: The outside and bearing walls are masonry walls without additional thermal insulation. The interior walls are masonry, as well. The roof is a timber construction with poor insulation. The energy performance of the building is substandard to actual demands (German Energieeffizienzklasse G). Prefab deep renovation solutions: Adding prefabricated facade elements (Fermacell), additional thermal roof insulation, thermal insulation of the basement ceiling, installation of new windows with triple glazing and installation of a new gas boiler. The energy saving target after deep renovation is 100 kWh/ m²a. The replication potential is high because the building type is very common in Germany and there are many buildings that have a lack of thermal insulation and HVAC systems that are not up- to date.
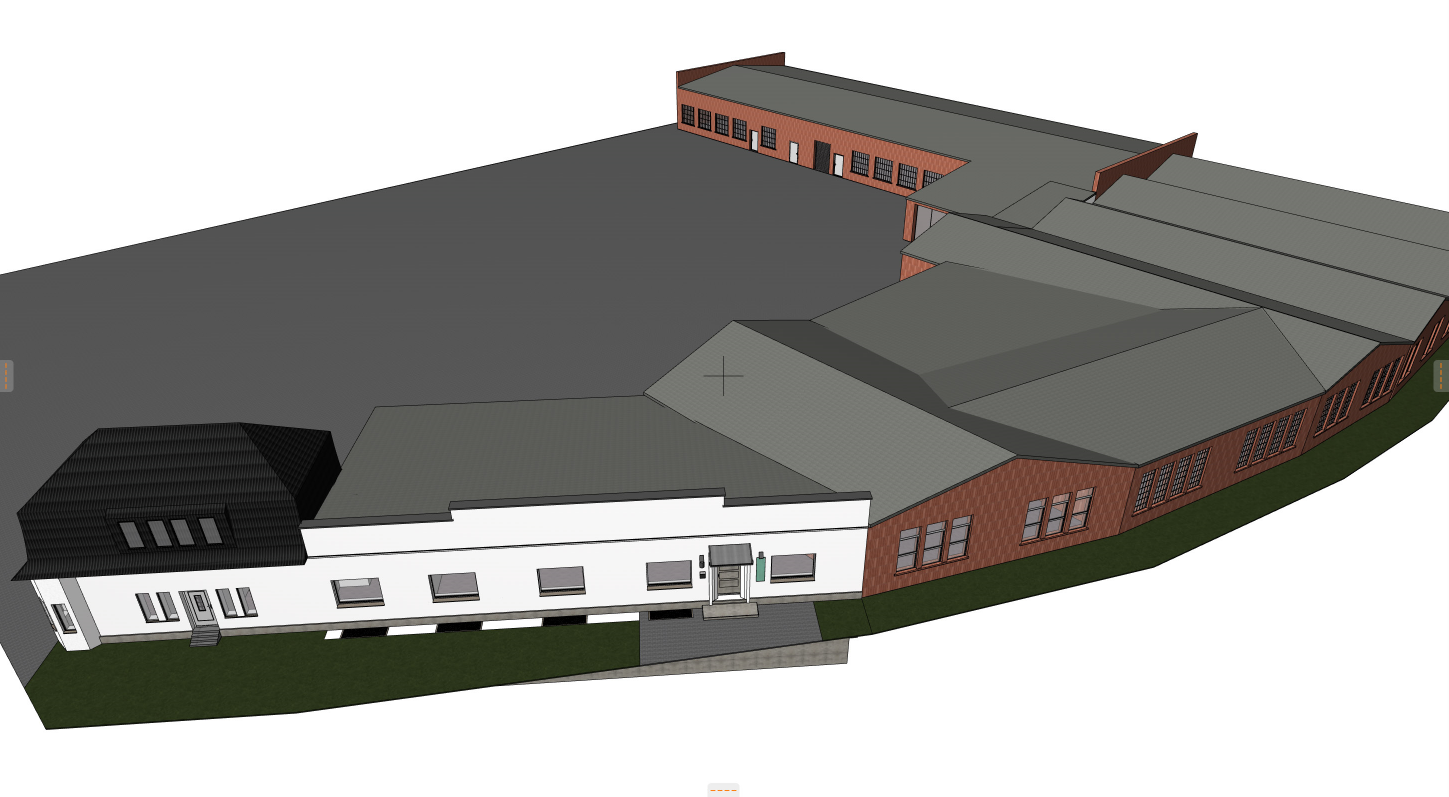
Implementation with P2ENDURE PnP solution
3L and Fermacell developed a façade system that was then pre-produced by a German general contractor and applied to the office building in Menden (Germany - close to the 3L headquarter). The building was shortly presented in the M24 Consortium Meeting in Rome and is replacing the former demonstration case in Soest. The office building is part of a larger group of buildings containing storage houses and areas with administrative use. Of course, the client was involved in the planning and development process and was prepared for realisation. This demo case is one of the first executed examples of this special type of facade. The replicability of the planned measures is extremely high as in the cases' neighbourhood there are similar buildings, all build between the years 1900 and 1930, too, and none of them have been modernised so far. Normally buildings from these decades reached an age now where no further investment seems to make any sense regarding ecologic feasibility. But regarding just this demo case an overall area of approximately 4.000 m² could be renovated in this manner.
After the execution of a laser scan and a mapping of the existing building including geometrical and thermal data a 3D BIM model was prepared and tender drawings were produced and iteratively checked and optimized by 3L, Fermacell and the general contractor. The BIM will support the ongoing planning and realization.
The facade of the Menden case is realised as a prefab light weight timber construction and was mounted within 4 hours. It contains a mineral thermal insulation and integrated channels for PnP HVAC ducts. In the façade a special climate component BlueMartin freeAir is integrated that regulates the humidity and air pressure of the interior. The ComfortEye technology to monitor the energy consumption and the indoor air quality before and after renovation was installed. Two sensors are measuring and gathering data that are sent and processed in Italy by P2Endure partner UNIVPM.
There is a high replicability potential not only in Menden, because there are many buildings in Germany and other European countries with the same typology and similar potential for the application of PnP solutions.
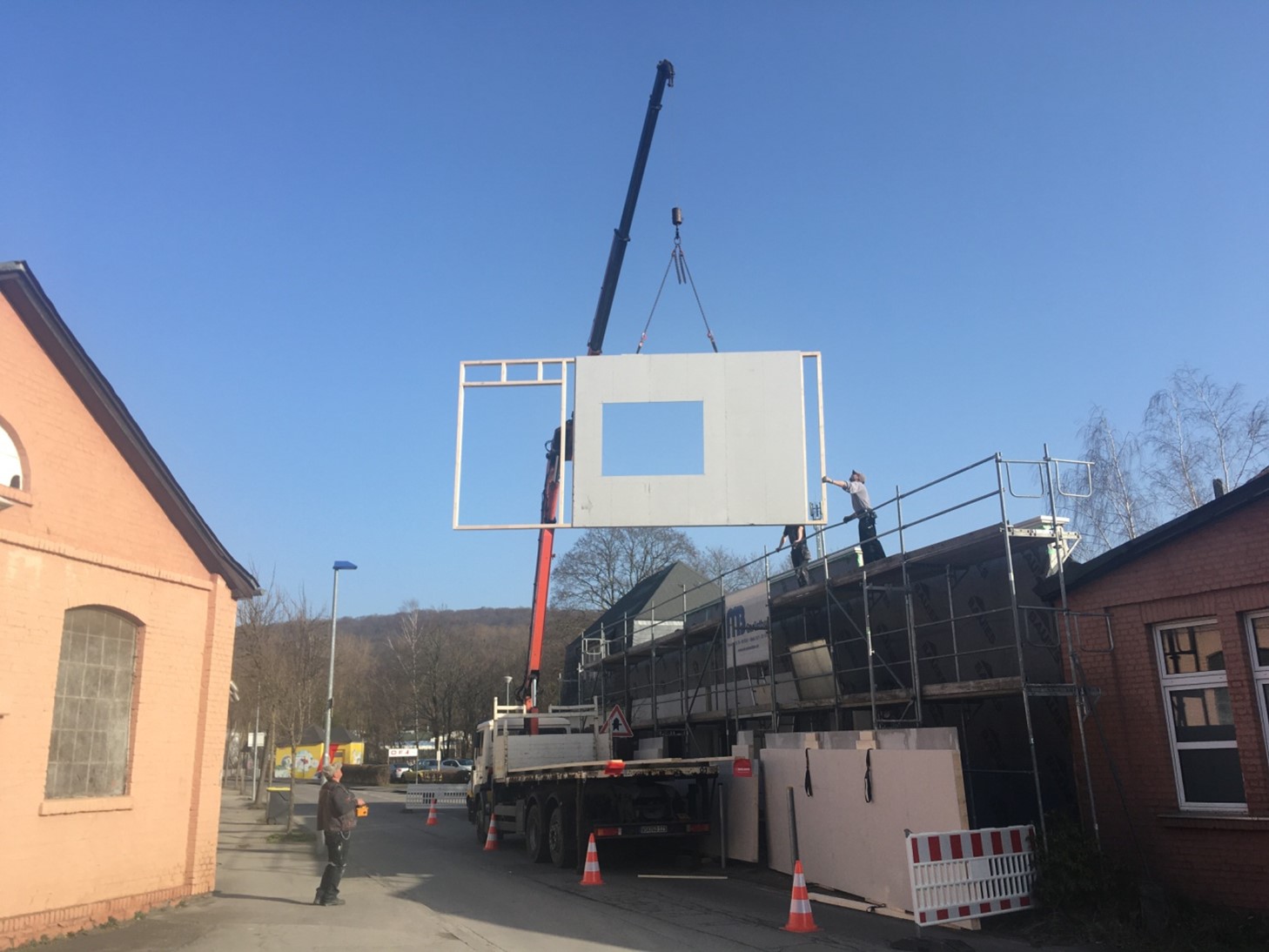
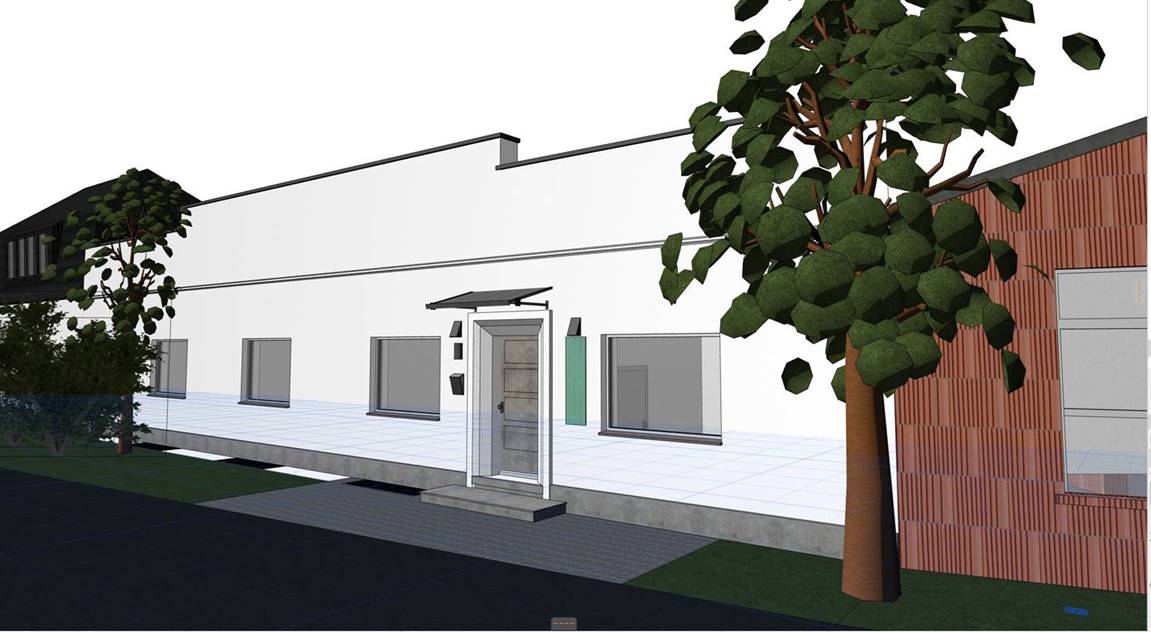